Thursday - May 25, 2006
The well drilling crew came today at 8 AM. We all gathered up chairs and drinks to watch the show. It was a job that any person with an interest in machinery at work would love. I told Richard it was his dream - heavy machinery, lots of noise and playing in dirt!
The trucks they brought were amazing. Absolute marvels of engineering. The actual well drilling rig was a hydraulic lift, a pressure tank, an air compressor, a storage area for pipes, a drill, a crane, a pipe wrench (super large one!), a massive screwdriver, and a winch! The other truck that held the pipes was also an 11,000 gallon water tank - they use the water under high pressure to aid in the drilling. The rest of it was used for extra pipe storage and the storage of various bits of equipment used in the drilling.
One thing I did notice. The trucks were engineered to "help" do all the jobs involved in drilling, lifting, and placing. The two men had assigned tasks and much work was automated scientific application of the tools provided. Everything was though of from the pipe wrench that was operated hydraulically to the simple tube used to store the two drill bits. It was interesting as I am a user of tools when I quilt and many tools women seem to use are clunky, outmoded and often not ergonomic or user friendly. I know that's a sexist statement but think on it...indoor vacuum cleaners - hoses, nozzles, machine lugged up and down steps...no grip handle, just a push handle and BAGS (although finally someone figured out bagless). But a shop vac for men...wheels that turn so it can go any direction...an engine that has great suction, no bag, just a dump bucket and so on.
Anyway. The first drill bit was nine inches wide - this is to dig a large hole so that the 6 inch casing can be installed. Once the drill reaches 80 feet, they switch to a drill of 6 inches. After they reach 80 feet, the casing is installed and then Bentonite, a type of quick setting concrete is poured down the outside of the casing to set it in place. Once the casing is in place, they continue drilling to reach the water.
We hit the top of the water table at about 190 feet but the pressure wasn't enough to support the submersible pump. We decided to drill deeper to get better pressure. We checked every 20 feet and finally at 250 feet we got the required pressure to run the submersible pump at peak efficiency. It took exactly 5 hours from start to finish to drill the 250 feet and put in the casing, waterpipes and bentonite.
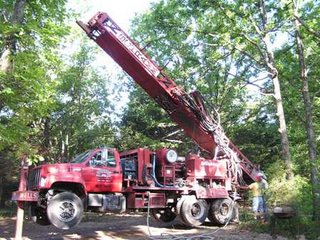
The crane starts to rise so that the trees can be trimmed and the drill can be placed.

Starting work. Walt is trimming the trees with branches that may interfere with the crane's operation.

The 9 inch drill bit is positioned and begins work.

A larger view of the whole area.

I'm watching the work...see the truck nearest me? That red "flatbed" is actually an 11,000 gallon watertank. The drillers use high pressure water to help speed the drill as it digs the hole.
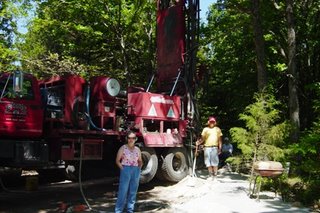
Me by the driller's rig.
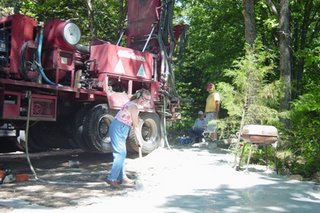
Me shoveling the "slurry" of ground limestone, sandstone and the water that is ejected from the hole as the drill digs.

The diesel engine that ran the drilling rig for 5 hours had a huge fan to vent the heat from the engine. The hot air blew up into this tree and eventually burned the leaves.

This was the final test of water pressure. After all the industrialized machinery to do the work, a simple stop watch and 1 gallon paint can are used to test pressure. At a signal, the paint can holder fills the can while the stopwatch holder times how fast it fills. The test was done 3 times at different depths before pressure was acceptable for the submersible pump. A pump needs water flowing at about 2 1/2 times its capacity so it will never have to be sucking air. My pump needed a minimum of 15 gallons per minute. We managed to get 25 gallons per minute.

The pipes are down the well and it is currently capped until the pressure tank and the submersible pump are installed.

A larger photo of the area to show where the well is in relation to the shed.

Echo and Flint came up for a time to visit. They didn't like the loudness of the diesel so I took them home after a while.
The well drilling crew came today at 8 AM. We all gathered up chairs and drinks to watch the show. It was a job that any person with an interest in machinery at work would love. I told Richard it was his dream - heavy machinery, lots of noise and playing in dirt!
The trucks they brought were amazing. Absolute marvels of engineering. The actual well drilling rig was a hydraulic lift, a pressure tank, an air compressor, a storage area for pipes, a drill, a crane, a pipe wrench (super large one!), a massive screwdriver, and a winch! The other truck that held the pipes was also an 11,000 gallon water tank - they use the water under high pressure to aid in the drilling. The rest of it was used for extra pipe storage and the storage of various bits of equipment used in the drilling.
One thing I did notice. The trucks were engineered to "help" do all the jobs involved in drilling, lifting, and placing. The two men had assigned tasks and much work was automated scientific application of the tools provided. Everything was though of from the pipe wrench that was operated hydraulically to the simple tube used to store the two drill bits. It was interesting as I am a user of tools when I quilt and many tools women seem to use are clunky, outmoded and often not ergonomic or user friendly. I know that's a sexist statement but think on it...indoor vacuum cleaners - hoses, nozzles, machine lugged up and down steps...no grip handle, just a push handle and BAGS (although finally someone figured out bagless). But a shop vac for men...wheels that turn so it can go any direction...an engine that has great suction, no bag, just a dump bucket and so on.
Anyway. The first drill bit was nine inches wide - this is to dig a large hole so that the 6 inch casing can be installed. Once the drill reaches 80 feet, they switch to a drill of 6 inches. After they reach 80 feet, the casing is installed and then Bentonite, a type of quick setting concrete is poured down the outside of the casing to set it in place. Once the casing is in place, they continue drilling to reach the water.
We hit the top of the water table at about 190 feet but the pressure wasn't enough to support the submersible pump. We decided to drill deeper to get better pressure. We checked every 20 feet and finally at 250 feet we got the required pressure to run the submersible pump at peak efficiency. It took exactly 5 hours from start to finish to drill the 250 feet and put in the casing, waterpipes and bentonite.
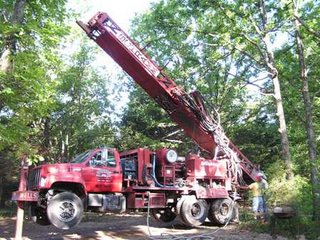
The crane starts to rise so that the trees can be trimmed and the drill can be placed.

Starting work. Walt is trimming the trees with branches that may interfere with the crane's operation.

The 9 inch drill bit is positioned and begins work.

A larger view of the whole area.

I'm watching the work...see the truck nearest me? That red "flatbed" is actually an 11,000 gallon watertank. The drillers use high pressure water to help speed the drill as it digs the hole.
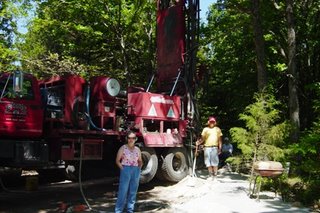
Me by the driller's rig.
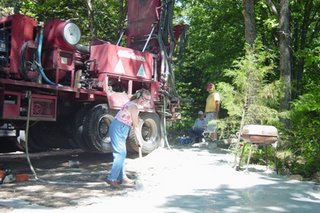
Me shoveling the "slurry" of ground limestone, sandstone and the water that is ejected from the hole as the drill digs.

The diesel engine that ran the drilling rig for 5 hours had a huge fan to vent the heat from the engine. The hot air blew up into this tree and eventually burned the leaves.

This was the final test of water pressure. After all the industrialized machinery to do the work, a simple stop watch and 1 gallon paint can are used to test pressure. At a signal, the paint can holder fills the can while the stopwatch holder times how fast it fills. The test was done 3 times at different depths before pressure was acceptable for the submersible pump. A pump needs water flowing at about 2 1/2 times its capacity so it will never have to be sucking air. My pump needed a minimum of 15 gallons per minute. We managed to get 25 gallons per minute.

The pipes are down the well and it is currently capped until the pressure tank and the submersible pump are installed.

A larger photo of the area to show where the well is in relation to the shed.

Echo and Flint came up for a time to visit. They didn't like the loudness of the diesel so I took them home after a while.
0 Comments:
Post a Comment
<< Home